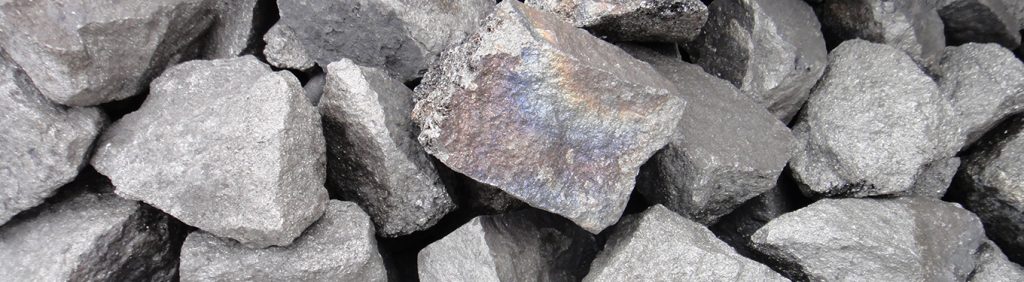
ferro silicon
Ferro Silicon is an alloy which is produced by combining iron and 15% to 90% of silicon. Ferro Silicon or FeSi is widely used in color or non-color metallurgy industry as an important deoxidizing material and besides this is used as a bud or spraut in the Moulding industry. Also, it is primarily used as a deoxidizing material in steel alloy manufacturing industries, in producing cast iron and steel, developing metallic structure and granulation in the molding of alloy and non-alloy cast irons, refurbishment of other Ferro alloys, and most importantly in the structure of nouvelle alloy steel.
Specification of Ferro Silicon (FeSi70-75%):
Silicon | 70-75% |
Al | 2% Max. |
Carbon | 0.15% Max. |
Sulphur | 0.05% Max |
Phospate | 0.05% Max. |
Melting Point | 1200°C – 1250°C |
Boiling Point | 2355°C |
Specification of Ferro Silicon (FeSi70-72% & 72-73%)
Si | 70-72% | 72-73% |
Al | 1% Max | 0.80% Max |
C | 0.15% Max | 0.12% Max |
S | 0.02% Max | 0.02% Max |
P | 0.04% Max | 0.04% Max |
Cr | 0.03% Max | 0.03% Max |
Ti | 0.02% Max | 0.02% Max |
Size: As per customer’s request ranging between 10 to 150mm
Packing: Loose in Bulk or in 1MT Big Bags as per customer’s request
Ferro Silicon is used for:
Steelmaking and foundries as a source of silicon in production of carbon steels, stainless steels, and other ferro alloys for its deoxidizing properties. Used in manufacturing silicon steel for electro-motors and transformer cores. It is used for inoculation of the iron. To prevent loss of carbon from the molten steel. In arc welding, ferro silicon can be found in some electrode coatings.
Uses
#Ferro silicon is mainly used as important deoxidizer in steel- making.
#This is used as alloy elements join agent, that are generally used in heat-resistant alloy steel, low bearing steel, steels, non-ferrous metal and electrician silicon-steel.
#Ferro silicon normally used as a chief reductant in ferroalloy production and chemical industry. Ferro silicon normally used as a chief reductant in ferroalloy production and chemical industry.
#Ferro silicon is also used in iron industry as inoculants and nodulizer.
Ferro Silicon can broadly be defined as an alloy of Iron and Silicon. It is a ferroalloy with a silicon % between 15-90 % by weight. Its melting point is about 1200 °C to 1250 °C with a boiling point of 2355 °C. The density of ferrosilicon decreases with increasing silicon content.
Ferrosilicon is used as a source of silicon in foundries and steelmaking. It is of great importance in the production of other ferrous alloys, carbon steels, and stainless steels, among other things. Ferrosilicon has excellent deoxidizing properties; it is these properties that help produce the above materials. Loss of carbon from the molten steel is thus prevented through the use of its deoxidizing properties. Ferro silicon is said to be an excellent heat blocker. Ferro silicon is also used to produce other Ferro alloys.
In manufacture of cast iron, ferrosilicon is used for inoculation of the iron to accelerate graphitization. Ferrosilicon can also be found in some electrode coatings used in arc welding. Silicon steel for transformer cores and electro-motors, silicon, as well as high-temperature-resistant and corrosion-resistant ferrous silicon alloys all makes great use of ferrosilicon.
Ferro silicon can be used to make other ferroalloys too. Ferrosilicon is also a basis for manufacture of pre-alloys like magnesium ferrosilicon (FeSiMg). It is also an important additive to cast iron for controlling the initial content of silicon. Ferrosilicon is also used in the Pidgeon process to make magnesium from dolomite.
FeSi is a highly power consuming product. FeSi needs almost 3 times power/electricity compared to SiMn & FeMn. As a result, the cost of electricity is the main proportion of the cost of FeSi (almost 65% of the total cost of production). A typical 9MVA furnace producing 16,500MT of SiMn & FeMn per year will produce only 7,200MT of Ferro Silicon. Therefore, even though we are strongest in the production of FeSi, it comprises of only 15% of our total production. The main grades produced by us are:
Quality:
- The typical quality issues related with Ferro silicon can be described as follows:
- Si % lower than specified
- Dust, Slag or Slag inclusions in the finished metal
- Poor luster with dull and unfinished surfaces of the packed alloy
- Undersize
- Powdering or weathering of the finished alloy when stored and exposed to air.
- Uneven distribution of Iron and Silicon in the finished alloy
Pioneer Carbide offers Ferro Silicon free from any of the above defects. The company enjoys a solid reputation for quality products among its customers. The company has committed itself to quality by employing strict quality control measures for the raw materials as well as the finished Ferro silicon. Every tapping of Ferro Silicon is tested for its specifications and quality compliance. The finished Ferro silicon is compact, has smooth surfaces on sides, free from slag inclusions or dust and has a metallic sound when dropped on its heap.
Products:
Ferro Silicon 77% Min:SILICON (Min %) – 77 ALUMINIUM (Max %) – 1.5 CARBON (Max %) – 0.1 PHOSPHORUS (Max %) – 0.06 CALCIUM (Max %) – 0.5 MANGANESE (Max %) – 0.5 SULPHUR (Max %) – 0.04
|
![]() |
Ferro Silicon 75% Min:SILICON (Min %) – 75 ALUMINIUM (Max %) – 1.5 CARBON (Max %) – 0.1 PHOSPHORUS (Max %) – 0.06 CALCIUM (Max %) – 0.5 MANGANESE (Max %) – 0.5 SULPHUR (Max %) – 0.04
|
![]() |
Ferro Silicon 72% Min:SILICON (Min %) – 72 ALUMINIUM (Max %) – 1.5 CARBON (Max %) – 0.1 PHOSPHORUS (Max %) – 0.06 CALCIUM (Max %) – 0.5 MANGANESE (Max %) – 0.5 SULPHUR (Max %) – 0.04
|
![]() |
Ferro Silicon 70% Min:SILICON (Min %) – 70 ALUMINIUM (Max %) – 1.5 CARBON (Max %) – 0.1 PHOSPHORUS (Max %) – 0.06 CALCIUM (Max %) – 0.5 MANGANESE (Max %) – 0.5 SULPHUR (Max %) – 0.04
|
![]() |
Ferro Silicon 65% Min:SILICON (Min %) – 65 ALUMINIUM (Max %) – 2 CARBON (Max %) – 0.1 PHOSPHORUS (Max %) – 0.06 CALCIUM (Max %) – 0.5 MANGANESE (Max %) – 0.5 SULPHUR (Max %) – 0.04
|
![]() |
Other Products:
Ferro Silicon Slag
- Shot & Grits for use in Steel Industries:
- Chilled Iron Shot
- Cast Steel Grits
- Steel Grits
- Steel Cut Wire Shot
- Stainless Steel Shot
- Iron Grits
- Stainless Steel Cut Wire Shot
- Steel Abrasive
- Cast Steel Shot
- Steel Shot
- Industrial Steel Grits
- Iron Steel Grits
- Iron Cut Wire Shot
- Steel Cut Wire Pellets
- Chilled Iron Grits
- Chilled Iron Shots
- Cut Wire Pellets
- Aluminum Shot
- Zinc Shot
- Copper Shot
- Lead Shot
- Metallic Abrasive
- Shot Peening Media
- Shot Blasting Media
Page-4-5